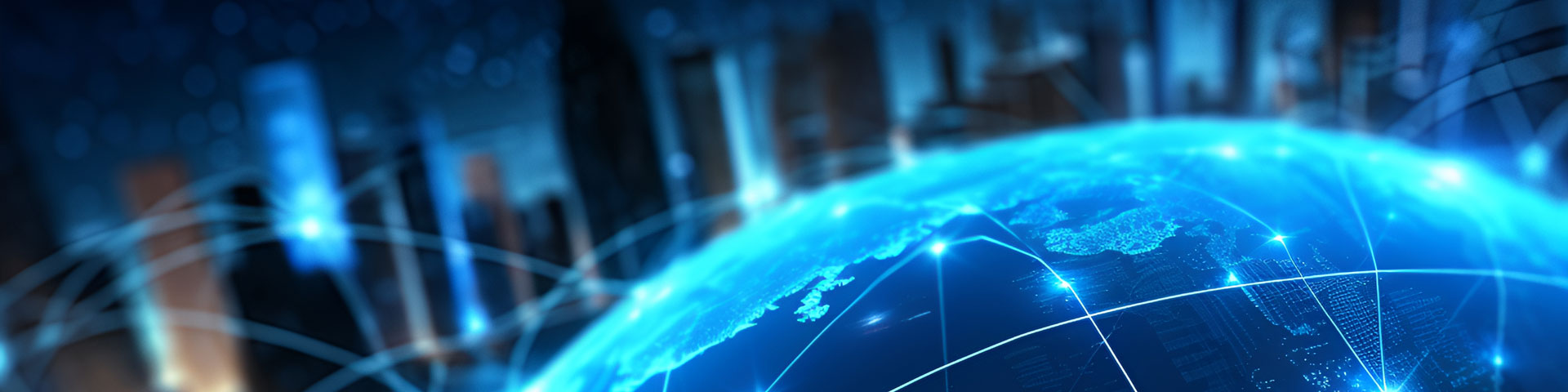
新闻中心
【专题分享】人工智能技术&数据价值
人工智能技术&数据价值+创新开展
导读
【AG凯发K8国际智慧|讲座】·人工智能技术&数据价值,本期为下篇冷冻水系统专题——优化控制策略(致谢:由于参考来源转载或改编,版权归原作者所有,在此对原作者表示感谢!)
基于建模的优化控制算法
先对各设备进行建模,在模型基础上构建冷冻系统运行优化问题,并采用各种优化算法对目标函数进行求解。(运用数学方法来分析/解决物理特性问题)随着算法的开展,越来越多的优化算法被运用到冷水机组的优化控制方法之中,其收敛性以及全局优化效果也越来越好,但本质上来说,这都是属于基于模型的优化方法。
基于模型的优化控制策略是建立系统或具体设备模型
模型主要功能:
(1) 模拟系统的能耗、费用以及系统对控制变量变化的反应;
(2) 可以获取设计变量与目标函数之间的关系;
(3) 控制策略以某种变量为优化变量,创建目标函数,并利用优化算法寻找目标函数的最优解;
在冷水机组系统中,优化变量一般为冷水机组启停状态、各台冷水机组分配负荷、冷冻水出水温度等参数;目标函数一般为室内温度、能耗或者费用等。
冷冻水系统模型类型
冷水机组物理模型和基于(专家/经验)数学模型
冷水机组的物理模型通常十分详细且精确,能够较为准确的反应冷水机组的性能,有利于控制策略的制定。然而在实际应用中,物理模型中许多参数往往难以测量。同时在对物理模型的控制方程进行求解时通常会十分复杂。因此基于物理模型的控制策略一般难以用于实际应用。绝大多数冷冻水系统仿真软件都是顺利获得搭建好物理模型来进行仿真。而冷水机组的经验模型相对简单,且计算成本一般可控,因此,更适合实际应用之中。
(1)基于物理模型的优化控制
-----物理模型中许多参数往往难以测量;物理模型的控制方程求解十分复杂。
(2)基于数学模型的优化控制
-----效果取决于冷水机组模型的质量以及优化算法的寻优效果。而在工况多变的实际应用中,很难始终保持拟合模型的精度。同时用于求解的寻优算法很难同时保持寻优效果与计算速度,而这两点对于冷水机组系统的优化控制、在线控制至关重要。
冷冻主机物理特性模型
(涉及比热容系数,空气传导热系数,空气/水流量换热等系数)
冷冻主机数学模型
由ENERGY PLUS+文献资料中的Engineering Referent。参考资料可知,对于离心冷水机组数学模型:
冷水机组的实际运行能耗是与PLR , Tcw. Tcond,。等参数相关的非线性函数,其中PLR是由中央空调系统运行所需冷负荷决定的,而Tcw , Tcond则是在冷水机组运行期间给定的温度控制设定值。
公式为:
冷却塔物理模型
变转速冷却塔的数学模型建立是基于经验的拟合性能曲线和厂家样本的性能数据或实验结果拟合而得。在建立冷却塔的性能曲线时,要第一时间得知冷却塔的一些额定参数,包括:冷却塔进口空气干球温度,最大风量,水量,风机功率,出口水温和设计状况下各的各参数。
公式中:Approach一一冷却塔出口水温与风机入口的空气温度之差(℃ )
FRair:一一空气流量率,为实际空气流量除以额定空气流量;
FRwater:一一水流量率,为实际水流量除以额定水量;
Twb一冷却塔进出口水温温差(℃ )
Tr一空气湿球温度(℃ );
C1-C35一一相互关系的系数。
水量与风量的改变均对冷却效果有较大影响,水量改变影响较大,几乎成线性关系,风量改变在风量较大时,对冷却效果影响较小,而在风量较小时则对冷却效果有较大影口向
冷却能力与空气湿球温度和入口水温均呈线性变化关系。
基于冷水机组性能图的优化控制策略
冷水机组的运行数据生成冷水机组的性能图,用于描述冷水机组在不同运行工况下的性能,并利用冷水机组性能图指导冷水机组的优化控制策略。
利用历史运行数据获取精度更高的冷水机组性能图,可实现冷水机组性能图对冷水机组的启停控制与负荷分配进行优化控制;利用运行数据对冷水机组性能图进行定期更新,进一步提高了冷水机组性能图的精度以及控制策略的优化效果。
基于性能图的优化算法:基于不同运行工况下的运行数据获取冷水机组性能图,并根据性能图寻找当前工况下的最佳运行状态。该优化算法避免了建模和寻优过程,计算快速,适合在线实时优化控制;但性能图是基于实际运行数据或仿真数据预先生成,用于在线实时搜索,且无法对性能图以外的工况进行优化控制,因此性能图对运行数据的质量数量和工况种类都有较高要求
在获取大量位于冷水机组性能包络面上的数据点之后,其拟合曲面可以近似认为是冷水机组性能包络面。冷水机组的性能包络面是冷水机组性能图的上边界线,越接近冷水机组性能包络面的数据点运行效率越高。
取得冷水机组运行性能包络图的具体步骤如下:
步骤一:依据大量有效的历史运行数据,分别生成各个不同工况下的冷水机组运行性能图;不同负荷下对应的系统瞬时COP的值,设置不同温度/温差。
步骤二:从冷水机组运行性能图中提取到不同工况下冷水机组的运行性能包络线。
步骤三:将所有工况下的冷水机组运行性能包络线组合成为冷水机组运行性能包络图。
基于冷水机组性能图的优化控制策略存在问题
1) 异常数据破坏性能图质量
----基于性能图的优化控制一般是基于不同运行工况下的运行数据获取冷水机组性能图。而在实际应用过程中,由于测量数据具有动态特性,并受到噪声干扰,具有很大的波动与误差,这就导致所获的性能图优化效果大大降低。
2) 运行数据不足或分布不均匀
----性能图是基于实际运行数据或仿真数据事先生成的,而在实际应用中,冷水机组的历史运行数据量不足或者运行数据分布不均匀的情况。历史运行数据量不足时,仅能取得不完整的性能图,影响后续的优化控制的效果。
3) 性能图更新与生成
-----冷水机组系统随着使用年限的变化,其运行性能会逐渐衰退,其性能图也会随之变化,因此需要对性能图进行定时更新才能保证其优化效果,而在线控制中对性能图进行更新与生成对性能图的生成速度有一定的要求。
基于冷水机组性能图的优化控制策略
现场采集的冷水机组的各个变量的测量值均是由传感器采集得到的,由于误差是不可避免的,因此现场采集到的变量的数据值与真实值就会存在一定的偏差。
由于传感器均存在大小不一的测量不确定性,因此会造成冷水机组冷冻水流量、冷冻水进水温度、冷冻水出水温度等测量值存在误差,进而导致冷负荷(冷量)的值存在误差。而冷负荷是很关键参数;在控制策略中作为逻辑判定,在最终计量COP的计量上都是很重要。
冷负荷测量值的偏差不仅会造成运行性能包络图获取的准确性,而且还会导致在包络图中无法精准地匹配到相应的运行数据点,进而造成控制策略对冷水机组的运行指导发生偏差从而无法使系统运行在最佳运行点上。
在实际应用中,冷负荷的值一般是顺利获得冷冻水总流量和冷冻水进出水温差计算而来,
冷负荷值的不准确是由冷冻水总流量和冷冻水进出水温度等变量的测量值不准确引起的。测量值的不准确的原因主要分为测量值异常和误差。而误差是持续存在的,因而可能会导致持续的不准确性,降低冷负荷测量值的可靠度。
数据融合+设备机理模型优化控制算法
数据融合是将冷负荷的直接测量值和间接测量值融合到一起,顺利获得判断冷负荷直接测量值和间接测量值的变化关系,重新构成一个冷负荷的融合值,以此来增强冷负荷测量结果的可靠性。
目标:对冷负荷的测量值进行修正
冷负荷值的直接测量与间接测量:
直接测量:根据冷冻水的总流量和冷水机组系统的冷冻水进出水温差计算出冷负荷的大小/流量计数据
间接测量:顺利获得建立冷负荷的拟合模型来对冷负荷的值进行预测,如下公式所示:
其中,α和β是间接测量冷负荷拟合模型的系数,可以顺利获得历史实测数据拟合得到。
数据融合算法关键点
1)检测并剔除数据异常值
检测方法:比较当前时刻冷负荷直接测量值的增量△Qdm,、与当前时刻冷负荷间接测量值的增量△Qim的差距。如果冷负荷直接测量值的增量△Qdm,与冷负荷间接测量值的增量△Qim的差距大于所定义的闽值时,则认为当前时刻的冷为了提高数据的质量,在数据融合的第一步中,需要从众多的冷负荷测量数据里将异常的冷负荷值剔除;检测方法有很多,常规方法是顺利获得增量判定原则。
负荷直接测量值为异常值;反之,则认为没有出现异常值。当冷负荷直接测量值异常时,则利用冷负荷间接测量值的增量进行修正,获取融合之后的冷负荷的大小。
2) 减少测量中噪声的影响
若当前时刻的直接测量值不是异常值时,可以用移动窗口算法(滑动平均)来减少测量噪声的影响。
3)消除系统误差的影响
系统误差往往会对冷负荷的直接测量值产生影响,由于系统误差相对恒定且变化较慢,因此系统误差会逐渐累积在Sdm,k中,进而影响冷负荷融合值的准确度。因此顺利获得计算冷负荷融合值和冷负荷间接测量值的差来判断是否产生了系统误差,如下公式所示。如果没有产生系统误差,则二者之差会在某一小范围内波动;如果产生了系统误差,即二者之差超出了合理的波动范围
4)数据融合的置信度
在完成对冷负荷的数据融合之后,需要对得到的冷负荷融合值进行评价,因此建立了数据融合的置信度来反映冷负荷融合值质量的高低。置信度的范围为0至1,置信度的值越接近1证明融合值的质量越高,越接近0证明融合值的质量越差。此外,顺利获得建立数据融合的置信度可以在测量值质量很差时发出警告,以便于对出现的故障及时进行处理。
Q5基地数据分析
数据拟合的关键点:
(1)数据梳理和分析
(2)拟合函数的构建形式
设备寻优策略
借助物联网数据采集手段,可以方便地获取制冷机组的实时运行数据,包括蒸发侧进出水温度、冷凝侧进出水温度、机组运行电流及功率、机组负载率( 或电流百分比) 等,顺利获得对实时数据的持续跟踪监测和对比分析,可以研判机组的制冷能力、加载速率、运行效率等性能水平,从而优先选择性能更优的机组投入使用。
系统级数据价值点
1. 实时数据反映系统实时运行工况,对制造中实时工艺参数要求高的客户;是这类客户迫切的需求点。类似于过程控制管理(实时跟踪制造环节/参数突变预报警功能)
2. 对能耗大户企业,顺利获得优化控制策略实现节能降本。但对能耗分析,节能依据需求高。所以,针对这类企业,需要把能耗分析这块做扎实,做准确
3. 某个行业要做得有深度,才能体现优势。以高效机房为例,能耗分析/能耗差分析其实是空白;
4. 数学模型系统级数据价值点:
构建精准度方面还有优化空间(从流体学角度,流速/阻力系统角度构建模型更能反映当前真实工况)