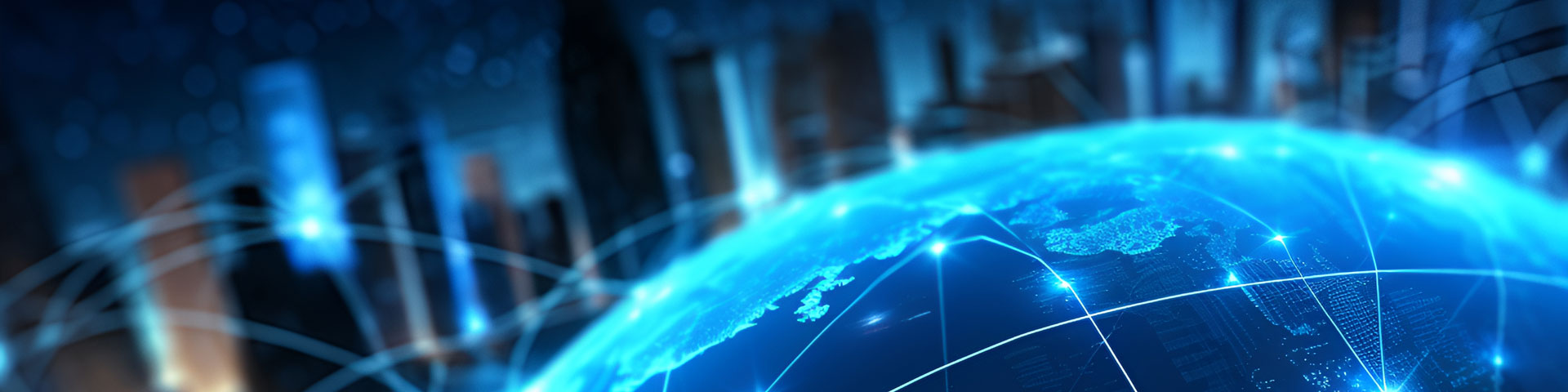
新闻中心
【智慧工厂】从精益工厂布局入手——提升生产效率
从精益工厂布局入手——提升生产效率
工厂布局简介
布局简介:布局(Layout),是一个组织为实现其工作目标、效益最大化,对其工艺、部门、设施设备和工作区进行的规划和实际定位、定置。
布局的意义:“结构决定功能”,每一种产品由于设计结构的差别,所具备的功能也不尽相同。
任何一个组织如果没有相应的组织架构,就不会具备相应的业务功能,达到相应效率和产出相应效益。
所以,没有合理的布局和流程,就不可能造就高效的生产系统。
布局的目的:
人: 提高工作热情;减少不必要动作和走动;
材料: 减少材料、产品的运输距离和搬运次数;减少中间制品;
管理: 简化管理;实现均衡生产;
利用率: 提高人和设备的利用率;提高空间利用率;
传统布局模式
传统布局的基本形式:
1、固定式布局(以产品为中心)
2、功能式布局(以设备为中心)
3、流程式布局(以流程为中心)流程式布局,是指按照加工工艺流程进行布局。
4、混合式布局(结合前三种布局)固定式、功能式和流程式布局三种布局的混合布局。俗称,混乱式布局。
传统布局的缺陷和不足:
1、大批量生产;
2、过多的在制品;
3、不必要的搬运;
4、生产不均衡;
5、生产计划排程难;
6、生产缺乏柔性;
7、埋没了员工的智慧和创造力,无法取得满足感;
8、不便于发现生产流程中的问题和浪费;
精益布局简介
精益布局,是以现状布局为基础, 顺利获得消除人、机、料、法、环(4M1E)各个环节上的浪费,来实现五者最佳结合的布局。精益布局的应用方法主要抓住“单件流”这一精益化的核心思想。
精益布局的应用方法:打破孤岛作战,在可能的地方开展陆续在流,减少孤岛作业工序和区域。
精益布局的五种模式:
1、串联式布局:
缺点: 对周转方式考虑较少; 对工序之间的联系考虑较少; 场地利用率考虑较少;
2、并联式布局: 适合一人操作两台设备; 步行及搬运距离短; 可以随时观察设备运作状态;
3、U型布局:
U型布局优点: 进料和出料口一致,异常信息可以及时传递; 一人操作3台以上的设备; 可以随时观察设备运作状况;
员工操作步行距离较近; 占用空间场地较小;
4、单元化布局:
单元化生产布局,是精益生产的一个模块,是当代最新、最有效的生产线设置方式之一,为日本以及欧美企业所广泛采用。这种方式使得小批多种生产残酷环境下的生产线几乎比流水线效果还好,因此被誉为“看不见的传送带”。
单元化生产方式:单元化生产,是指将设备和厂房以特定的顺序安排,使材料和零件由1个或极少的作业者以最小的搬运完成部分或者全部生产过程。把4M进行合理的安排,进行更好的单件流生产;
只要有需要,可以进行单件流操作,1个员工也可以完成整个操作过程; 通常按产品族或者按工艺流程分组;通常采用 “U” 型布局。
优点:更有效的目视化管理; 生产过程头尾相接; 最小化走动的距离; 提高了工序间的平衡; 避免了孤岛操作。
能够实行单人多工位操作; 加强了员工之间的研讨; 更好的发现异常情况; 更容易实现高频率小批量物料补充需求 ;
适应节拍T/T的变化; 生产计划和人员配备的变化更容易实现。
布局的基本规则: 将设备与工位靠在一起; 移走工作路径上的障碍物; 单元里面的宽度大约为1.5m; 排除可能产生WIP(标准在制品)的环节;
流程的起点与终点靠得很近; 在工作场所避免上上下下、前前后后往返传输; 将一些基本的作业步骤安排在一起。
5、L型布局:
优点: 一人操作两台以上的设备; 可以随时观察设备运作状况; 员工操作步行距离较近; 操作物料流动方向与原物流路线一致。
精益布局的作用:
1、提高工序间平衡能力;
2、消除搬运;
3、提高场地利用率;
4、站立或走动操作,提高工作效率,减少职业伤害;
5、降低劳动强度;
6、提高作业质量和效率;
7、适应多品种少批量生产;
8、可以跟随产量的变化增减人员;
9、改善作业环境等。
精益布局与传统布局的区别:
精益布局的原则:
1、统一原则:
内容:把工序四要素4M:“人”、“机”、“材料”、“作业方法”,有机统一起来,并充分保持平衡。
理由:一旦四要素没有统一协调好,作业容易割裂,会延长停滞时间,增加物料搬运的次数。所以应充分考虑四要素的平衡的基础上进行。
2、最短距离原则:
内容:配置时要使搬运距离、时间最短。
理由:移动距离越短、物料搬运所花费的费用和时间就越短。
3、物流顺畅原则:
内容:使工序没有堵塞,物流顺畅。
理由:使物流不要倒流和交叉迂回。要设法使物流像水从高处向低处那样顺畅。
4、利用空间原则:
内容:为有效利用空间,立体利用空间。
理由:在材料、零件等仓库堆积一定是极狭窄放置的。因此把仓库设计成网架,以达到高效率地利用三角空间。
5、安全满意原则:
内容:布置得使工作人员既能安全又能轻松作业。
理由:确保作业人员的安全和减轻疲劳是非常重要的。材料的移动、旋转等都会出现不安全状况,抬升、卸下货物会加剧作业疲劳、应尽量减少。
6、灵活机动原则:
内容:适应变化,随机应变,采取灵活措施。理由:面对各工序的变化、增减等变化,尽可能随机应变、见机行事。
实现精益布局的步骤
1、现场布局图绘制:结合企业工艺布局图,绘制企业制造现场的设备、工装、模具、电器部分、工位器具、安全通道、员工工作位置等生产要素的相对布局位置和布局结构,
各个绘制要素的尺寸按照统一的缩放比例进行描叙,但相对精确尺寸和本身实际尺寸不需要明确的标明。
2、根据产品族确定分析对象:确定要分析的产品对象,获取一个产品的生产工艺过程作为主线来综合考虑布局结构的合理性和通用性。
3、收集过程块关键信息:获取现场实际存在的最全面的信息,他们是实现精益布局的基础条件,这些重要数据的收集可以帮助我们详细辨别生产过程中外部信息和内部信息,
并顺利获得信息的梳理和结构化,作为精益布局实施的依据。如:产品种类清单;周期时间;产品换模/换型时间; 设备有效工作时间;生产批量大小;操作工数量;有效工作时间;废品率等。
4、生产过程节拍分析及定拍:在布局结构分析的过程中, 节拍是一个非常重要的分析信息,他的作用是确定生产能力、工作量大小等,从而给给各个产品系列设计需求的人机料法环(4M1E)等各个生产要素。
5、各个过程块信息特征分析:对各个过程块的信息进行整理和分析,获取有效的特征信息来支持新的布局结构,新的布局结构与旧的布局结构之间的对比和调整都是依据具体的现场信息来提供决策的依据。
例如:对比工序节拍与生产节拍,实施新布局必须重点解决的瓶颈工序;设备配置数量的确定;换模/换型时间的分析和改善。
6、现场库存状况分析:顺利获得现场观察